Ceramics have been an integral part of human civilization for thousands of years. From the simple clay pots used in ancient times to the sophisticated components in modern technology, ceramics have evolved significantly. Today, we distinguish between traditional ceramics, which include everyday items like pottery and bricks, and advanced ceramics, which are used in high-tech applications such as aerospace, medical devices, and electronics.
Understanding the differences between traditional and advanced ceramics is crucial for anyone involved in material selection and product development. Knowing these differences can help you choose the right material for your specific needs, ensuring optimal performance and longevity. Whether you are a manufacturer, engineer, or simply curious about the materials that make up our world, this knowledge is valuable.
Table of Contents
Definition and Composition
Traditional Ceramics
Materials Used
Traditional ceramics are made from naturally occurring raw materials. The primary materials used in traditional ceramics include:
- Clay: A naturally occurring material composed mainly of fine-grained minerals.
- Silica: Also known as silicon dioxide, found in sand and used to improve the strength and durability of ceramics.
- Feldspar: A group of minerals used to lower the melting temperature of the mixture during the firing process.
Common Products
Traditional ceramics are typically found in everyday items that have been used for centuries. Some common products made from traditional ceramics include:
- Pottery: Items such as vases, bowls, and other household vessels.
- Bricks: Used extensively in construction for building walls and structures.
- Tiles: Employed in flooring, roofing, and wall coverings for their durability and aesthetic appeal.
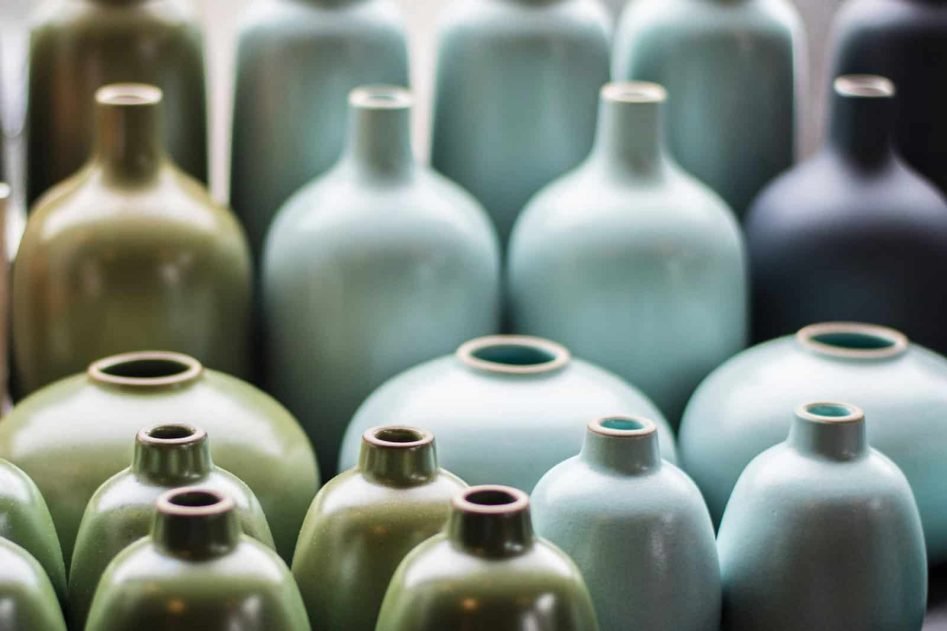
Advanced Ceramics
Materials Used
Advanced ceramics, also known as technical or engineering ceramics, are made from highly refined and pure raw materials. These materials are engineered to achieve specific properties that meet high-performance requirements. The primary materials used in advanced ceramics include:
- Alumina (Aluminum Oxide): Known for its hardness, wear resistance, and thermal stability.
- Zirconia (Zirconium Oxide): Noted for its high strength, toughness, and fracture resistance.
- Silicon Carbide: Valued for its exceptional thermal conductivity, hardness, and chemical resistance.
- Silicon Nitride: Renowned for its high strength and thermal shock resistance.
Common Products
Advanced ceramics are utilized in high-tech and demanding applications where their superior properties offer significant advantages. Some common products made from advanced ceramics include:
- Industrial Manufacturing Components: Components such as wear-resistant parts, seals, and bearings are used in heavy machinery and manufacturing equipment. Their durability and ability to withstand harsh conditions make them ideal for continuous use in industrial environments.
- Molds and Dies: Advanced ceramics are used to produce high-precision molds and dies for the manufacturing industry. These molds and dies must endure high temperatures and repeated mechanical stress without deforming or wearing out.
- Renewable Energy Components: In the renewable energy sector, advanced ceramics are used in wind turbine bearings and solar panel substrates. Their ability to resist environmental degradation and maintain performance over long periods is crucial for the reliability and efficiency of renewable energy systems.
- Semiconductor Industry: Advanced ceramics play a vital role in the semiconductor industry, where they are used in substrates and insulating components. Their thermal stability and electrical insulation properties are essential for the production of reliable and high-performance electronic devices.
- Automotive Industry: In the automotive industry, advanced ceramics are used in engine components, sensors, and brake systems. These materials can withstand high temperatures and mechanical stress, improving the performance and reliability of automotive systems.
Understanding the materials and typical products of both traditional and advanced ceramics is the first step in recognizing their distinct characteristics and applications.
Manufacturing Processes
Traditional Ceramics
Methods
The manufacturing processes for traditional ceramics are relatively straightforward and have been used for centuries. The primary methods include:
- Molding: Shaping the ceramic material into the desired form using molds. This can be done manually or with the help of machines.
- Firing: Heating the shaped ceramic in a kiln to a high temperature, which causes the materials to harden and develop their final properties. This step can involve multiple firing stages, depending on the desired characteristics.
Techniques
Several traditional techniques are employed to shape and form traditional ceramics:
- Hand-Building: A manual method where clay is shaped by hand into the desired form. Techniques include pinching, coiling, and slab construction.
- Wheel-Throwing: Using a potter’s wheel to shape the clay. The wheel spins the clay while the potter shapes it with their hands and tools.
- Slip Casting: Pouring liquid clay (slip) into plaster molds. The plaster absorbs water from the slip, leaving a layer of solid clay on the mold walls, which is then fired to create the final product.
Advanced Ceramics
Methods
The manufacturing processes for advanced ceramics are more complex and precise, designed to achieve the high-performance properties required for advanced applications. The primary methods include:
- Powder Processing: The raw materials are processed into fine powders, which are then mixed with binders and additives to create a uniform mixture.
- Sintering: The shaped ceramic powders are heated to a temperature below their melting point, causing the particles to bond together. This process enhances the material’s strength and density.
- Hot Pressing: Combining heat and pressure to form and densify the ceramic material simultaneously. This method results in ceramics with superior mechanical properties and reduced porosity.
Techniques
Several advanced techniques are employed in the production of advanced ceramics:
- Chemical Vapor Deposition (CVD): A process where gases react on a heated substrate to form a thin ceramic coating. This technique is used to create high-purity, high-performance ceramic films.
- Physical Vapor Deposition (PVD): A process where material is vaporized in a vacuum and deposited onto a substrate to form a thin film. PVD is used for coating components with hard, wear-resistant ceramic layers.
- Sol-Gel Processing: A chemical process that transforms a liquid (sol) into a solid (gel). This method is used to produce ceramic materials with precise compositions and microstructures, often at lower temperatures than traditional methods.
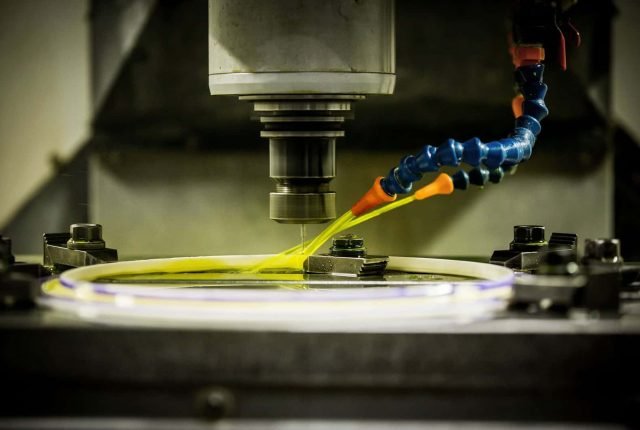
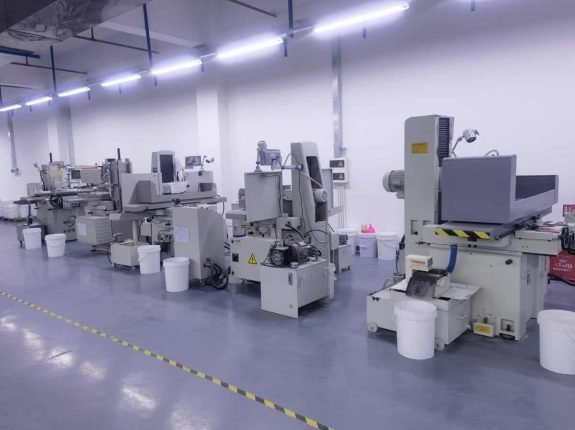
Understanding the differences in manufacturing processes between traditional and advanced ceramics is essential for selecting the right material for specific applications. These processes directly influence the properties and performance of the final ceramic products.
Traditional Ceramics
Mechanical Properties
Traditional ceramics typically exhibit the following mechanical properties:
- Brittle: Traditional ceramics are generally brittle, meaning they can fracture easily under stress without significant deformation.
- Porous: These ceramics often have a porous structure, which can affect their strength and durability.
Thermal Properties
Traditional ceramics have moderate thermal properties:
- Moderate Thermal Stability: While they can withstand moderate temperatures, traditional ceramics are not suitable for extremely high-temperature applications. They can tolerate heat better than many polymers but are outperformed by advanced ceramics in high-temperature environments.
Electrical Properties
Traditional ceramics are primarily used as electrical insulators:
- Insulators: They have high electrical resistivity, making them effective in preventing the flow of electrical current. This property is why they are commonly used in applications like insulators for power lines and other electrical components.
Advanced Ceramics
Mechanical Properties
Advanced ceramics are known for their superior mechanical properties:
- High Strength: These ceramics can withstand high mechanical stresses, making them ideal for structural applications.
- Hardness: Advanced ceramics like silicon carbide and alumina are extremely hard, which makes them suitable for wear-resistant applications such as cutting tools and abrasives.
- Wear Resistance: Their high hardness contributes to excellent wear resistance, ensuring longevity and durability in demanding environments.
Thermal Properties
Advanced ceramics excel in thermal performance:
- High Thermal Stability: They can maintain their properties at very high temperatures, which is essential for applications in aerospace, energy, and industrial processes.
- Low Thermal Expansion: Advanced ceramics exhibit low thermal expansion, meaning they undergo minimal dimensional changes when subjected to temperature variations. This property is critical for precision applications where dimensional stability is required.
Electrical Properties
Advanced ceramics offer diverse electrical properties, making them suitable for a range of electronic applications:
- Conductors: Some advanced ceramics, like silicon carbide, can conduct electricity and are used in electronic devices.
- Semiconductors: Ceramics such as silicon carbide and gallium nitride have semiconducting properties, making them valuable in power electronics and sensors.
- Insulators: Advanced ceramics are also used as insulators in high-voltage and high-frequency applications due to their excellent dielectric properties.
- Piezoelectric: Certain ceramics can generate an electric charge in response to mechanical stress, known as piezoelectricity. This property is exploited in sensors, actuators, and transducers.
Material | Hardness | Strength | Thermal Conductivity | Electrical Insulation | Wear-restistance | High-Temperature Resistance | Corrosion Resistance |
Al2O3 | High | High | Middle | High | High | High | Middle |
ZrO2 | Middle | High | Low | Middle | High | Middle | Middle |
Si3N4 | High | High | Middle | Middle | High | High | High |
SiC | High | High | High | Low | High | High | High |
AlN | Middle | Middle | High | High | Middle | Middle | Middle |
The distinct properties of traditional and advanced ceramics highlight their suitability for different applications. While traditional ceramics are valuable for everyday items and construction materials, advanced ceramics offer enhanced performance for high-tech and industrial applications.
Applications
Traditional Ceramics
Common Uses
Traditional ceramics have been used for centuries and are still widely employed in everyday items and construction due to their accessibility and ease of production. Common uses include:
- Household Items: Traditional ceramics are used to make pottery, dishes, vases, and decorative items. Their aesthetic appeal and functional properties make them staples in homes worldwide.
- Construction Materials: Bricks, tiles, and cement are essential components in building and construction. Traditional ceramics provide structural integrity and durability to buildings and infrastructure.
Limitations
Despite their widespread use, traditional ceramics have limitations that restrict their applications in more demanding environments:
- Brittleness: Their tendency to fracture under stress limits their use in applications requiring high mechanical strength and toughness.
- Porosity: The porous nature of traditional ceramics can lead to weaknesses, especially in environments where moisture resistance is crucial.
- Moderate Thermal Stability: Traditional ceramics cannot withstand extremely high temperatures, making them unsuitable for high-temperature applications found in certain industrial processes and advanced technologies.
Advanced Ceramics
High-Tech Uses
Advanced ceramics are engineered to meet the rigorous demands of high-tech and industrial applications. Their superior properties make them indispensable in several advanced fields:
- Aerospace: Advanced ceramics are used in components such as turbine blades, heat shields, and thermal protection systems. Their ability to withstand extreme temperatures and mechanical stress makes them ideal for aerospace applications where reliability and performance are critical.
- Automotive: In the automotive industry, advanced ceramics are used in engine components, sensors, and brake systems. These materials can endure high temperatures and mechanical stress, enhancing the performance and reliability of automotive systems.
- Electronics: Advanced ceramics serve as substrates, insulators, and semiconductors in electronic devices. Their excellent electrical properties and thermal stability are crucial for the reliable operation of microelectronics and power electronics.
- Energy: In renewable energy systems, such as wind turbines and solar panels, advanced ceramics are used for their durability and efficiency. They play a crucial role in components that must resist environmental degradation and maintain high performance over long periods.
- Industrial Manufacturing: Components such as wear-resistant parts, seals, and bearings are essential in heavy machinery and manufacturing equipment. Advanced ceramics provide the durability and resilience needed for continuous operation in harsh industrial environments.
- Semiconductor Industry: Advanced ceramics are vital in the semiconductor industry for substrates and insulating components. Their thermal stability and electrical insulation properties are essential for producing reliable and high-performance electronic devices.
Advantages in Critical Applications
The advantages of advanced ceramics in critical applications stem from their unique properties:
- High Strength and Hardness: These properties ensure that advanced ceramics can withstand mechanical wear and stress, extending the lifespan of components in demanding environments.
- Thermal Stability: Their ability to maintain performance at high temperatures makes them suitable for applications in aerospace, automotive, and energy sectors.
- Electrical Properties: The diverse electrical properties of advanced ceramics make them versatile for various electronic applications, from insulating substrates to semiconducting components.
- Chemical Resistance: Advanced ceramics’ resistance to corrosion and chemical attack allows them to perform reliably in harsh environments, such as chemical processing and industrial manufacturing.


The distinct applications of traditional and advanced ceramics highlight their respective strengths and limitations. While traditional ceramics are essential for everyday and construction uses, advanced ceramics excel in high-tech and industrial applications where superior performance is required.
Cost and Availability
Traditional Ceramics
Cost Factors
The cost of traditional ceramics is influenced by several key factors:
- Raw Materials: Traditional ceramics are made from abundant and relatively inexpensive raw materials such as clay, silica, and feldspar. The widespread availability of these materials helps keep costs low.
- Production Methods: The manufacturing processes for traditional ceramics, such as molding and firing, are well-established and efficient. Techniques like hand-building and wheel-throwing are labor-intensive but have been optimized over centuries to minimize costs.
Market Availability
Traditional ceramics are widely available in the market due to their low cost and ease of production. They are commonly found in:
- Construction: Bricks, tiles, and cement are staple materials in the construction industry, readily available and affordable.
- Household Items: Pottery, dishes, and decorative ceramics are easily accessible to consumers and are produced on a large scale to meet demand.
Advanced Ceramics
Cost Factors
The cost of advanced ceramics is generally higher than that of traditional ceramics due to several factors:
- Material Purity: Advanced ceramics require highly refined and pure raw materials to achieve the desired properties. The processing of these materials to remove impurities and achieve specific compositions can be costly.
- Manufacturing Complexity: The production of advanced ceramics involves sophisticated techniques such as powder processing, sintering, and hot pressing. These methods require precise control and advanced equipment, contributing to higher manufacturing costs. Techniques like Chemical Vapor Deposition (CVD), Physical Vapor Deposition (PVD), and sol-gel processing add further complexity and cost.
Market Availability and Niche Markets
Advanced ceramics are less widely available than traditional ceramics and are often used in specialized applications. Their market presence is characterized by:
- High-Tech Industries: Advanced ceramics are essential in high-tech sectors such as aerospace, automotive, electronics, and energy. These industries require materials with superior properties, justifying the higher costs.
- Niche Markets: The unique properties of advanced ceramics make them suitable for niche markets where specific performance criteria are crucial. This includes applications in semiconductor manufacturing, renewable energy, and industrial machinery, where the benefits of advanced ceramics outweigh their higher costs.
The distinct cost and availability profiles of traditional and advanced ceramics reflect their different uses and value propositions. While traditional ceramics are affordable and widely used in everyday applications, advanced ceramics offer unparalleled performance for specialized and high-tech applications, justifying their higher costs.
Environmental Impact
Traditional Ceramics
Resource Extraction
The production of traditional ceramics involves the extraction of raw materials such as clay, silica, and feldspar from the earth. This process can have several environmental impacts:
- Land Degradation: Mining for raw materials can lead to the disruption of natural landscapes, soil erosion, and habitat destruction.
- Water Use: The extraction and processing of these materials often require significant amounts of water, which can strain local water resources.
Energy Consumption in Production
The manufacturing of traditional ceramics typically involves high-temperature firing processes, which consume substantial amounts of energy:
- Kilns: Traditional ceramics are fired in kilns that reach temperatures of up to 1,000 degrees Celsius or higher. The energy required to maintain these high temperatures often comes from non-renewable sources, contributing to greenhouse gas emissions.
- Carbon Footprint: The energy-intensive nature of ceramic production results in a considerable carbon footprint, impacting the environment through the release of carbon dioxide and other pollutants.
Advanced Ceramics
Sustainability
Advanced ceramics offer several environmental benefits due to their sustainable attributes:
- Recyclability: Many advanced ceramics can be recycled at the end of their lifecycle, reducing waste and conserving resources. Recycling processes can recover valuable materials for reuse in new ceramic products.
- Eco-Friendly Processes: Innovations in the manufacturing of advanced ceramics have led to more eco-friendly processes. Techniques such as low-temperature sintering and energy-efficient production methods help reduce the environmental impact of ceramic manufacturing.
Long-Term Durability and Impact
The long-term durability of advanced ceramics contributes to their environmental sustainability:
- Longevity: Advanced ceramics are highly durable and resistant to wear, which means they have a longer service life compared to traditional materials. This reduces the need for frequent replacements and minimizes waste.
- Energy Efficiency: In applications such as electronics and energy, advanced ceramics can improve energy efficiency. For example, ceramic components in renewable energy systems and electronic devices help enhance performance and reduce energy consumption, leading to lower environmental impact over time.
The environmental impact of traditional and advanced ceramics reflects their different production processes and lifecycle attributes. While traditional ceramics involve significant resource extraction and energy consumption, advanced ceramics offer sustainable benefits through recyclability, eco-friendly manufacturing, and long-term durability.
Conclusion
In conclusion, understanding the differences between traditional and advanced ceramics, from their properties and applications to their cost and environmental impact, is essential for making informed decisions in material selection and product development. By choosing the right type of ceramic for specific applications, industries can achieve optimal performance, efficiency, and sustainability.
If you have any questions or need assistance in selecting the right ceramic material for your application, please contact us. Our team of experts is ready to help you find the perfect solution to meet your needs. We are committed to providing high-quality advanced ceramic components tailored to your specific requirements. Contact us today to discuss how we can support your projects and enhance your products with the exceptional properties of advanced ceramics.